Утилизация послеспиртовой мелассной барды, несмотря на высокий расход пара, может быть весьма выгодна. Мелассная послеспиртовая барда является полноценной средой и самым дешевым сырьем для получения из нее бетаина (ацидина), глутаминовой кислоты и
глутамата натрия, как усилителя вкуса Е-621 (Цена 60 руб за 1 кг). Так, содержание глутаминовой кислоты в послеспиртовой барде составляет 2,3% на сухое вещество.
Как и при работе с сепарационными щелоками сахарных заводов, глутамат натрия и бетаин можно
получать двумя методами:
-
химическим,
-
ионитным.
Методом кислотного гидролиза С. С. Пойвин еще в 1940 г. получил из
концентрированной мелассовой барды бетаин (ацидин) и глутаминовую кислоту.
Для получения бетаина и глутаминовой кислоты химическим методом
мелассную барду сгущают до содержания
сухих веществ 75% и гидролизуют концентрированной соляной кислотой в
течение 30—40 мин при температуре 105—106 °С. Гидролизат очищают от
примесей активированным углем, фильтруют и упаривают. Из упаренного
фильтрата кристаллизуют бетаин (ацидин), а из маточного раствора получают
глутаминовую кислоту и глутамат натрия, как услитель вкуса Е-621.
При ионитном методе выделения глутаминовой кислоты и бетаина
мелассную барду
разбавляют в два раза конденсатом и пропускают через ионитовую фильтрационную установку с
синтетическими смолами, обладающими высокой обменной емкостью. На
вофатитовых катионитах адсорбируется бетаин, а на анионитах — глутаминовая
кислота. Иониты регенерируют соляной кислотой, в результате чего получают
солянокислый бетаин (ацидин) и глутаминовую кислоту, из которых после
очистки, упаривания и кристаллизации получают товарную продукцию.
На Лохвицком спиртовом комбинате ешЁ с 1952 г. освоено получение из барды
бетаина (ацидина) и глутамата натрия. Для производства этих продуктов на
комбинате оборудованы две промышленные установки, одна из которых работает
по ионитному способу, а другая по химическому.
Получение солянокислого бетаина и глутамата натрия химическим методом.
На основе длительных экспериментов на Лохвицком заводе разработана
технология получения из барды путем кислотного гидролиза глутаминовой
кислоты и бетаина (рис. 33).
Барда, упаренная до содержания 75% сухих веществ, подогревается в сборнике
/ и насосом 2 через мерник 3 подается в.
реактор 5„ Сюда же из мерника 4 поступает соляная кислота уд. веса
1,15. Соотношение барды и кислоты 1 : 0,7.
В реакторе с паровой рубашкой создается и поддерживается температура
105—106 °С. В процессе гидролиза в течение 30— 40 мин в осадок
выпадают гумины и часть минеральных солей (хлористый калий и др. ).
Гидролизат спускают в аппарат 7 с охлаждающей рубашкой, в котором при
медленном охлаждении до 25—30 °С дополнительно выпадает хлористый калий.
Осадок — смесь солей калия и гуминов — отделяется на фильтре 8
и может быть использован в качестве удобрения. Полученный фильтрат
поступает в промежуточный сборник 9, из которого после разбавления
водой насосом 10 передается на осветление активированным углем в
аппарат 11.
Осветление проводят при температуре 70—80°С. Затем фильтрат охлаждают до
40—50 °С и фильтруют. Осветленный раствор, собранный в сборник
осветленного раствора ацидина 13, засасывается на циркуляционной
вакуум-выпарной аппарат, состоящий из кипятильника 14, сепаратора
15, трубчатого конденсатора 16, нейтрализатора паров 17,
приемника солей 18 и сборника солянокислого конденсата 19.
Упаривание проводят при температуре не выше 56—57 °С, во избежание потерь
глутаминовой кислоты, до удельного веса раствора кислоты 1,32—1,33.
Выпавшая соль представляет собой смесь хлористых солей К, Na,
Са, Мg, хлоргидрат бетаина и называется сырой
солью ацидина. Вместе со щелоком она переводится в кристаллизатор 21,
оборудованный мешалкой и охлаждающей рубашкой. Из сборника масса
поступает на центрифугу 22, где отделяется сырая соль ацидина, а
маточный раствор, содержащий глутаминовую кислоту, собирается в сборник
фильтрата глутаминовой кислоты 23.
Получение бетаина (ацидина). Состав сырой соли зависит от качества мелассы
и содержит 4,3—5,3% связанного азота; зольность ее 48—54%. Сырую соль
переводят в закрытый аппарат с мешалкой и обрабатывают спиртом (0,15—0,2
л на 1 кг сырой соли).
Спирт отделяют на закрытой центрифуге 22, собирают в сборнике
щелока 26, откуда передают на регенерацию (на спиртовой завод).
Отжатую соль переводят в реактор 27, обрабатывают технической
соляной кислотой, в которой растворяется солянокислый бетаин, но плохо
растворяются хлористые соли калия и натрия. Разделение проводят либо на
центрифуге, либо на фильтре 8. Эти соли могут быть использованы в
качестве удобрения после нейтрализации межкристальной соляной кислоты
дефекатом с сахарного завода.
Раствор ацидина собирается в сборнике 28, откуда засасывается в
вакуумный выпарной аппарат.
Кислые конденсаты с содержанием 8 — 10% НС1 передают в
общий сборник 20, откуда перекачивают на спиртовой завод для
использования при подкислении мелассовых рассиропок.
Полученная после упаривания кристаллическая масса имеет светло-желтый цвет
и называется желтой солью ацидина.
Желтую соль ацидина переводят в сборник 21, охлаждают до 20—25 °С для
максимального выделения кристаллов, затем отделяют кристаллы от маточника
на друк-фильтре 8, а маточник, еще содержащий ацидин и КСl,
возвращают 3—4 раза на первую выпарную станцию. Далее следуют такие
процессы: растворение в воде желтой соли ацидина, осветление водного
раствора ацидина активированным углем в аппарате 30 при температуре
80—90 °С; отделение активированного угля на центрифуге 22,
кристаллизация при 0—5 °С в кристаллизаторе 21, отделение
кристаллов на центрифуге 22 и промывка спиртом в аппарате 31
с последующим отжатием спирта на фильтре. Промывка спиртом может быть
проведена и на закрытой центрифуге 22, что несколько увеличит
расход спирта, но сократит число операций.
В настоящее время на две промывки расходуется 0,15— 0,18 л спирта
на 1 кг ацидина.
Чистый влажный продукт высушивают в закрытой сушилке 34 при температуре
60-70 °С (лучше под вакуумом), расфасовывают и упаковывают.
Получаемый ацидин полностью отвечает техническим условиям на медицинский
препарат.
Получение глутаминовой кислоты. Маточный раствор, собранный в сборнике
23, прокачивают насосом 10 через трубчатый подогреватель
38 в реактор 39, разбавляют водой в соотношении 1 : 1 и при
температуре 100—105 °С осветляют активированным углем.
Перед отделением активированного угля раствор охлаждают до 40—50 °С; так
как хлорвиниловая фильтровальная ткань при повышенной температуре выходит из строя.
Осветленный раствор, собранный в сборнике 40, упаривают на выпарном
аппарате до уд. веса 1,3. Упаренный раствор переводят в аппарат 41,
обрабатывают крепкой соляной кислотой и сливают в аппарат 21 с
рубашкой. В этом аппарате поддерживается постоянная температура около О°С.
В течение 120—130 ч выкристаллизовывается солянокислая глютаминовая
кислота.
Кристаллы отделяют на закрытой центрифуге 22. Маточный кислый
раствор, содержащий другие аминокислоты мелассы (кроме глютаминовой),
через сборник 42 направляют в сборник 20, разбавляют кислым
конденсатом и направляют в спиртовой цех. Глютаминовую кислоту, снятую с
центрифуги, растворяют в воде, обрабатывают активированным углем в
осветлителе 44, уголь отделяют на друк-фильтре 5, а осветленный
раствор кислоты из сборника 45 насосом 10 направляют в
аппарат 46 и нейтрализуют раствором соды до рН 3,2. Чистый раствор
готовят в аппаратах 47, 48 и 49.
Кристаллизация глютаминовой кислоты проводится в течение пяти суток при
температуре около нуля в кристаллизаторе 21. Выпавшие кристаллы
глютаминовой кислоты отделяют на центрифуге 22, а маточник
возвращают (в зависимости от содержания в нем азота) через аппарат 23
на начальные стадии процесса.
Кристаллы глутаминовой кислоты, содержащие незначительное количество
(2,0—4,5%) поваренной соли, для ее отделения растворяют в горячей
дистиллированной воде в сборнике 53, затем в этом же аппарате
охлаждают в течение 2—4 ч и центрифугируют, сушат в полочной (или
вакуумной) сушилке 57 и расфасовывают.
Получаемая по описанной схеме глутаминовая кислота отвечает требованиям
ВТУ на медицинскую глутаминовую кислоту.
Для получения глутамата натрия кристаллы глутаминовой кислоты из сборника
52 необходимо обработать в нейтрализаторе 46 эквивалентным
раствором соды или едкого натра, упарить раствор и выкристаллизовать на
холоду. Эти процессы могут быть проведены в аппарате из некорродирующей
стали.
Все аппараты для получения ацидина изготовляют из материалов, стойких
против коррозии соляной кислотой. Применимы, стекло, фарфор, графит марки
АТМ, винипласт, полиэтилен, диабаз, некоторые сорта резины, фаолит, а из
металлов — тантал и относительно стойкий кремнистый чугун (для
изготовления насосов). За исключением тантала и графита все остальные
материалы малотеплопроводны.
Стекло и особенно фарфор очень чувствительны к резкой перемене
температуры, плохо поддаются ремонту. Поэтому все аппараты, в которых не
проводятся теплообменные процессы, изготовляются из стали с последующей
гуммировкой или фаолитированием или из винипласта, а емкости защищают
диабазовыми плитками на диабазовой замазке.
Теплообменные аппараты изготовлены из графитовых труб АТМ или выложены
плитками из этого же материала на различных замазках. Аппараты 46
могут быть выполнены из нержавеющей стали.
Выход ацидина более постоянен, чем выход глютаминовой кислоты. Из барды,
полученной после переработки 1 тонны мелассы по химическому способу,
получают 17 — 17,5 кг ацидина.
Выход глутаминовой кислоты сильно колеблется и зависит от качества
мелассы, ее происхождения, сроков ее производства и пр. На мелассе,
полученной при переработке свежей свеклы, он составляет около 2% к весу
мелассы, а при работе на мелассе, полученной от переработки гнилой свеклы
(содержание азота в мелассе менее 1,5%), выход глутаминовой кислоты падает
до 0,5—0,7% к весу мелассы, что приводит к значительному повышению ее
себестоимости.
Расход соляной кислоты на 1 кг продукта с учетом возврата
солянокислого сокового конденсата составляет около 10 кг и зависит
от выхода глутаминовой кислоты.
Производство бетаина и глутаминовой кислоты по ионитному методу.
Свежую барду, освобожденную от дрожжей, разбавляют до содержания 5% сухих
веществ, осветляют активированным углем и фильтрат после отделения ют угля
последовательно пропускают через четыре колонки: первая колонка
заполняется сульфоуглем, вторая — вофатитом II, третья — анионитом ЭДЭ-10П
и четвертая — вофатитом II. Раствор, вытекающий из последней ионитной
колонки, содержит 2,5% сухих веществ.
Все катиониты регенерируют нормальной соляной кислотой. Элюат (регенерат)
первого катионита (СаСl) сливается в
канализацию, а элюаты второго и третьего катионита смешиваются.
Технологическая схема производства представлена на рис.1.
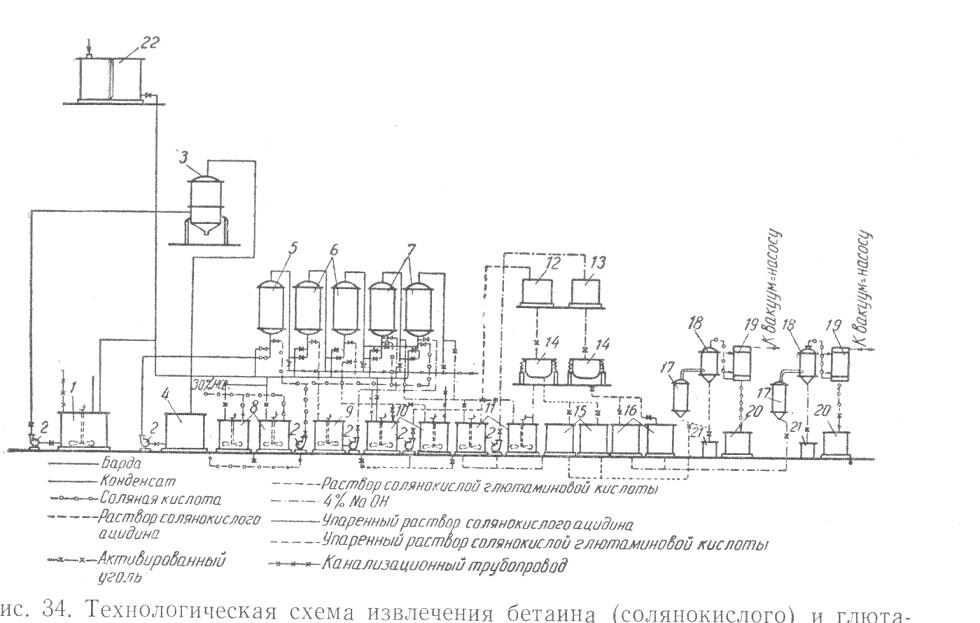
Рис 1. Технологическая схема извлечения бетаина (солянокислого) и
глутаминовой кислоты (солянокислой) ионитами из послеспиртовой мелассной
барды:
1 — сборник для осветления барды; .2 — центробежные насосы; 3 —
чулочный фильтр для барды; 4 — сборник отфильтрованной барды; 5 —
сульфоугольный фильтр; 6'— катионитовые фильтры; 7 — анионитовые фильтры;
8 — сборники для 30%-ной НС1; 9 — сборник для 4%-ной
NаОН; 10 — сборники раствора
солянокислого ацидина; 11 — сборники раствора солянокислой глютаминовой
кислоты; 12 — напорный сборник раствора солянокислого ацидина;
13 — напорный сборник раствора солянокислой глютаминовой кислоты;
14 — центрифуги; 15 — сборники отфильтрованного раствора
соляно-кислого ацидина; 16 — сборники отфильтрованного раствора
солянокислой глютаминовой кислоты; 17 — трубчатые однокорпусные
циркуляционные выпарки; 18 — сепараторы к ним; 19 —
трубчатые конденсаторы; 20 — сборники солянокислого конденсата;
21 — кристаллосборник; 22 — сборник конденсата.
В сборник 1 поступает свежая послеспиртовая мелассная барда со спиртового
завода и туда же подается равное количество конденсата или промывной воды
с одной из фильтрационных станций, а также активированный уголь.
Расход угля в зависимости от применяемой марки колеблется от 3 до 5% от
веса сухих веществ барды.
Насосом 2 раствор барды прокачивается через чулочный фильтр 3
в сборник 4. Из сборника отфильтрованная барда прокачивается
через сульфоугольный фильтр 5, катионитовые фильтры 6 и анионитовые
7. В сборниках 8 подготавливают 30%-ный раствор НС1.
После пропуска заданного количества барды (из расчета нагрузки: на
сульфоуголь — 10 л/л, на катионит — 5 л/л, на анионит — 12
л/л) со скоростью 0,75 л/л -ч фильтры отмывают конденсатом из
сборника 22, а затем соляной кислотой.
Регенерацию анионита проводят едким натром или аммиаком.
Во избежание потерь глутаминовой кислоты извлечение ее из анионита также
проводится с помощью нормальной соляной кислоты с последующей обработкой
анионита раствором едкого натра.
Элюаты сульфоугля сбрасывают в канализацию, элюат от катионита собирают в
сборниках 10, а от анионита — в сборниках 11. Если растворы
сильно окрашены, в эти сборники подают активированный уголь. Уголь
отделяют затем на центрифугах 14 или на фильтре 3, а элюаты
сливают соответственно в сборники 15 и 16.
Растворы раздельно упаривают под вакуумом на циркуляционных выпарных
аппаратах 17. Раствор солянокислого бетаина упаривают до густой
кристаллической массы, которая собирается в кристаллосборнике 21.
Раствор глютаминовой кислоты упаривают на выпарной станции до удельного
веса 1,3 (содержание сухих веществ 70— 72%).
В результате получается густой сироп светло-коричневого цвета следующего
химического состава (в %):
-
азота 4,1—4,5,
-
золы 0,1—1,5,
-
глицерина 50—51.
Материалом для изготовления ионитных колонн служит винипласт или
гуммированная сталь, а выпарные аппараты изготовляют из кислотостойких и
достаточно теплопроводных материалов.
После соответствующих испытаний работниками Лохвицкого спиртового
комбината были сконструированы и изготовлены опытные образцы выпарных
установок. Каждая из них состоит из кипятильника, сепаратора,
кристаллосборника и поверхностного конденсатора.
Для изготовления аппаратов служит графитовый материал АРМ, выпускаемый
Новочеркасским электродным заводом.
Упаривание кислых элюатов, содержащих 40—45 г сухих веществ в 1
л, проводят в однокорпусных вакуумных выпарных аппаратах.
Расход ионита, особенно анионита, чрезвычайно высок. При непрерывной
работе анионита ЭДЭ-10П он должен быть полностью сменен через 3—4 месяца.
Большой расход анионита объясняется условиями его работы (воздействие
барды, воды, соляной кислоты, едкого натра), вызывающими нагревание хорошо
развитой поверхности гранул анионита, что влечет за собой растрескивание,
измельчение и унос частиц анионита из аппарата.
В ближайшие годы на одном из крупных спиртовых заводов, перерабатывающих
мелассу, предусмотрено создание производства из мелассовой барды по методу
кислотного гидролиза до 1000 тонн глутамата натрия и 1400 т
бетаина (ацидина) в год.
Производство глицерина из мелассной барды.
При сбраживании мелассы на спирт в бражке как
побочный продукт спиртового брожения образуется глицерин в количестве 5—6
кг/м3 бражки (до 10% от веса полученного спирта). После отгонки
спирта из бражки глицерин переходит в барду и составляет 4,5—6,5% к весу
сухих веществ барды.
Извлечение глицерина из мелассной барды было организовано на Лохвицком спиртовом
комбинате по следующей схеме.
Барду, полученную из бражки, после сепарации дрожжей фильтруют и упаривают
на пятикорпусной выпарной установке (первые три корпуса под давлением, а
последние — под вакуумом) до концентрации 75 — 80% сухих веществ. Удельный
вес барды 1,38 — 1,40, вязкость при 20°С около 15, а при 90 — 95°С — менее
0,5 пз. Расход пара на получение 1 тонны концентрированной барды
составляет 1,2 — 1,15 тонн. Состав упаренной барды (в %): глицерина 6,
золы 15, органического остатка 54.
Элементарный состав органических соединений (в %):
-
углерод ................. 27 — 28
-
водород ................. 3,5 — 5
-
сера ................... 0,1 — 0,3
-
кислород .............. 22 — 24
-
азот . .................. 2,5 — 4,5
Теплотворная способность (низшая) 2500—2700 ккал.
Концентрированную барду окончательно упаривают до содержания сухих веществ
95% в автоклавах с подвижной поверхностью нагрева и затем отгоняют
содержащийся в сгущенной барде глицерин с водяным паром под вакуумом.
Полученный после дистилляции глицерин-сырец для очистки и осветления
обрабатывают ионитами. Состав глицерина (смеси глицеридов) после очистки
(в %): глицерина 93—95, органического остатка 0,6 — 1,4 (в том числе азота
0,2 — 1,1); цвет — от светло-желтого до бесцветного.
На 100 дал вырабатываемого спирта может быть получено около 50 кг
глицерина, или 16 кг на 1 тонну перерабатываемой мелассы.
Несовершенство технологии и аппаратурного оформления процесса
(периодическая кубовая дистилляция) обусловливает низкое качество
получаемого на Лохвицком заводе глицерина и недостаточный его выход (50 —
60 %). Однако при устранении этих недостатков для заводов большой мощности
(7 — 10 тыс. дал спирта в сутки) производство глицерина будет
перспективным.
На мелких заводах барду целесообразно концентрировать, после чего
транспортировать ее в цистернах на крупные заводы для дальнейшей
переработки.
Получение бардяной золы и энергетического тепла.
После выделения
глицерина из концентрированной барды остаток (гудрон) разбавляют до 75%
сухих веществ и сжигают в камерных топках специальных паровых
котлов-утилизаторов Ла-Монта, оборудованных устройствами для улавливания
летучей и расплавленной золы. Упаренная барда, как указано выше, содержит
до 60% органических веществ, а из минеральных солей— около 40% поташа.
Теплотворная способность сгущенной барды составляет, как указано, более
2500 ккал/кг. Полученный при сжигании барды пар давлением 25 ати направляется на турбогенераторы, после чего расходуется на
производственные нужды. Таким образом, в результате сжигания барды можно
использовать до 75% образующегося тепла и получить на каждые 100 дал
спирта 3,9 т пара и около 10 кВт мощности на валу
турбины.
При сжигании барды зола улавливается в дымоходах котла, а наиболее мелкие
ее фракции — в электрофильтре. Бардяная зола имеет следующий состав (в %):
-
поташ (К2СО3) .............. 38—42
-
сода (Na2СО3)
............... 18—22
-
сернокислый калий (К2SО3)
........ 12--14
-
хлористый калий (КС1) .......... 12—15
-
фосфорнокислый калий (КзР04) ...... 0,5—1,5
-
нерастворимый осадок ........... 6—8
Из 1 т мелассы получается около 65 кг бардяной золы. При
переработке этой золы в соли калия и натрия можно получить: поташа 35
кг, соды 15 кг, К2SО4
5 кг, КС1 5 кг. Поташ находит применение в стекольной
промышленности при изготовлении высококачественного хрусталя.
Использование бардяной золы в дрожжевом производстве.
Бардяная зола
успешно применяется на ряде дрожжевых заводов (Киевский, Одесский и др.) в
качестве дополнительного питания для дрожжей при .переработке малозольных
меласс.
По данным исследований, за последние годы количество малозольной мелассы
(содержание золы ниже 8%) составляет более 25%, а в годы высокого урожая
свеклы и длительного сезона сахароварения этот процент значительно
повышается.
При переработке малозольной мелассы получается низкий выход дрожжей и
ухудшается их качество. Это обусловливается недостаточностью в среде
макро- и микроэлементов минерально-органических питательных комплексов.
Низкая концентрация минеральных веществ особо отрицательно сказывается в
начальный период процесса накопления дрожжей.
В прессованных дрожжах, выработанных из малозольной мелассы, содержание
золы не превышает 1,6%, и поэтому дрожжи обладают пониженной подъемной
силой, темной окраской и плохой стойкостью.
Применение бардяной золы в количестве 1,12—1,5% по весу мелассы (в
зависимости от содержания золы в мелассе) в качестве дополнительного
минерального комплекса обеспечивает повышение выхода дрожжей и улучшает их
качество. На Киевском дрожжевом заводе бардяная зола смешивается с
суперфосфатом и сульфатом аммония и в виде солевого раствора задается в
дрожжерастильный чан в начале процесса. Повышение концентрации минеральных
солей в начальных стадиях накопления дрожжей создает благоприятные условия
для их роста и развития. При этом повышаются буферные свойства среды, что
предохраняет от нарастания кислотности в дрожжерастильном чане.
Бардяную золу целесообразно применять на всех дрожжевых заводах и при
переработке нормальных по зольности меласс, что должно способствовать
повышению выхода дрожжей и улучшению их качества.
Производство метана и витамина В12 из послеспиртовой мелассной
барды.
При сбраживании барды без доступа кислорода, в
анаэробных условиях, органические вещества (углеводы, жиры и др.)
распадаются на метан, углекислый газ, водород и ряд органических кислот.
Метан и водород используются в качестве топлива. Выход водорода составляет
примерно 1% по объему, а выход метана — около 10 м3 на 1 м3
сбраживаемой барды с содержанием СО2 около 27%.
Брожение ведут в закрытых бродильных аппаратах с получением на 1 м3
емкости аппарата до 3,5—7 м3 газа в сутки. Для брожения
применяют сапрофитные анаэробы и метанообразующие бактерии. Первые
разлагают сложные органические вещества барды с образованием кислот
жирного ряда (уксусной, муравьиной, масляной и др.), а вторые разлагают
жидкость с образованием метана и углекислоты.
При анаэробном сбраживании барды содержание в ней органических веществ
снижается с 8,5 до 4%. Наряду с образованием метана бактерии метанового
брожения накапливают в 1 м3 бродящей среды до 0,5 г
витамина В12.
Режим брожения: при 35 °С около 10 дней, а при 57 °С около 5 дней.
По окончании метанового брожения содержание органических веществ в барде
снижается наполовину, а биологическая потребность в кислороде — на 70—80%,
чем достигается значительное обезвреживание сточных вод барды.
В последнее время в ФРГ ведутся исследования по выращиванию на мелассовой
барде актиномицетов с целью получения антибиотиков и витаминов, а также по
анаэробному сбраживанию мелассовой барды для получения метана для летучих
кислот.
Проведенными опытами установлено, что мелассовая барда при аэрировании
может быть использована для выращивания микроорганизмов (актиномицетов или
бактерий), продуцирующих антибиотик — биомицин и витамин В12.
По этим исследованиям, в опытах с Streptomyses
olivaceus за 50 ч ферментации в 1 л барды накопление
витамина В12 составило 1,1 мг, а при использовании в
качестве продуцента Bactilius megatherrium через
20 ч ферментации в 1 л барды получено 0,7 мг витамина В12.
Установлено также, что относительно высокое содержание золы в барде не
тормозит размножения продуцента витамина В12.
Получение цианистых соединений.
Для получения синильной кислоты и
аммиака барду после выделения глицерина направляют на коксование в реторты
из шамотного кирпича при температуре 700 °С.
В результате коксования выделяются триметиламин, окись углерода, вода и
углерод. Газы из реторт направляют в перегреватели-рекуператоры, нагретые
до 1050 °С, где из триметиламина при температуре 800—1000 °С образуется
синильная кислота и выделяются аммиак, метан, водород и углерод. Газы
очищают от смолы, нафталина и сажи в трубчатых холодильниках и абсорберах
с серной кислотой, где связывается аммиак.
Синильную кислоту отмывают водой с температурой 10°С в колпачковых
колоннах и отгоняют, а оставшиеся газы сжигают в печах.
Газообразную синильную кислоту направляют на абсорберы, наполненные
раствором едкой щелочи. Полученный раствор цианистой соли фильтруют и
концентрируют под вакуумом, а выпавшие кристаллы отделяют
центрифугированием, сушат и упаковывают. Раствор сульфата аммония из
кислотных абсорберов фильтруют, кристаллизуют, кристаллы отделяют на
центрифугах, а затем сушат и упаковывают.
Бардяной уголь выгребают из реторт, выщелачивают горячей водой, после чего
раствор фильтруют, выпаривают и выкристаллизовывают соли калия и натрия.
При этом на каждую тонну переработанной барды получают (в кг):
-
цианистый калий
.............. 22,5
-
сернокислый аммоний ............ 17,5
-
поташ
................... 46,0
-
сода
.................... 11,5
-
сульфат калия
............... 3,0
-
хлористый калий
.............. 10,5
Из бардяного угля при обработке соляной кислотой можно также получить
активированный уголь.
В последнее время в химической промышленности освоено более рентабельное
производство цианидов и аммиака путем синтеза азота воздуха, в связи с чем
производство этих ценных продуктов из барды может оказаться
малоперслективным.
Получение бардяного угля.
Наименее совершенным методом утилизации
мелассовой барды является ее сжигание в печах с получением бардяного угля,
так как при этом используется только зола, а ценные органические вещества
теряются при сгорании.
Для сжигания барды ее упаривают в многокорпусной выпарке до содержания
сухих веществ 20%, после чего направляют в бардосжигательную печь. В
испарительной части печи за счет тепла газов, полученных при сжигании
барды во втором отделении печи, происходит испарение воды, благодаря чему
барда сгущается до 60% и сгорает без дополнительной затраты топлива.
В последнее время предложена печь для одновременного непрерывного сгущения
и сжигания мелассовой барды. Печь представляет собой чугунный
воронкообразный герметически закрытый сосуд, обогреваемый газом. В центре
сосуда проходит вращающийся полый вал, на котором укреплены
разбрызгивающие насадки и скребки. Внизу сосуд оканчивается спускной
трубой с двумя попеременно открывающимися затворами. Барда поступает
сверху в полый вал и через разбрызгивающие насадки стекает по стенкам
сосуда, а готовый бардяной уголь непрерывно снимается с поверхности сосуда
скребками, поступает в спускную трубу и оттуда выгружается попеременно
открывающимися затворами.
Выход бардяного угля составляет 7% от веса мелассы.
На ряде спиртовых заводов Польской Народной Республики переработку
мелассовой барды осуществляют по следующей схеме (рис. 3).
Сепарированная или несепарированная бражка поступает в колонну 4,
снабженную циркулятором. Из бражной колонны барда поступает в
нейтрализатор 5, где нейтрализуется известью. Нейтрализованная и
отстоявшаяся барда направляется при помощи насоса 14 в
трехкорпусную выпарную установку, работающую под давлением. Затем барда
последовательно проходит через первые три корпуса выпарки, упариваясь при
этом до содержания 30% сухих веществ, после чего перекачивается на
сжигание в испарительную башню 7 конвейерной печи 8. Насосом 6
барда нагнетается в форсунки, установленные в верхней части башни.
Распыление производится при давлении около 4 ати. Распыленная барда
попадает в башню 7, встречая на своем пути отходящие из печи горячие газы
(с температурой около 200°С), которые через трубу 12 выводятся в
атмосферу. Упаренная в башне барда поступает на под 9
бардосжигательной печи и при помощи скребкового конвейера 10
перемещается по нему, подвергаясь дальнейшему концентрированию и сгорая.
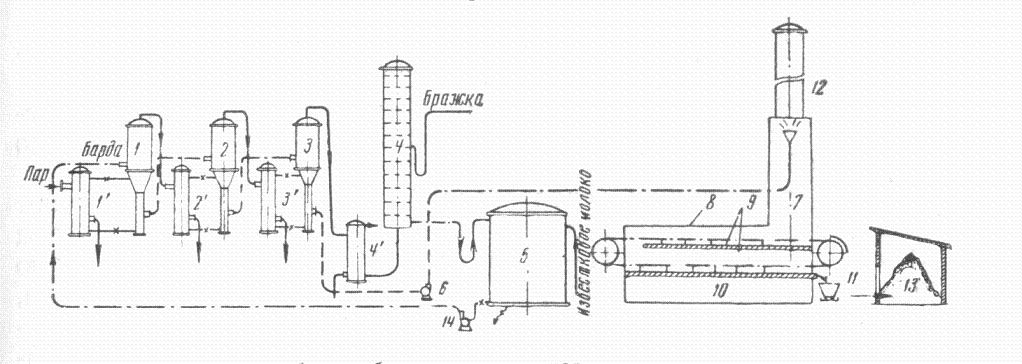
Рис. 3. Схема переработки | сжигания барды на спиртовых заводах Польской Народной
Республики:
1, 2, 3 - корпуса выпарной установки; 4 — циркуляционная
колонна; 5 — нейтрализатор; 6 — насос; 7 — испарительная башня;
8 — конвейерная бардосжигательная печь; 9 — под печи; 10 —
скребковый транспортер; 11 — вагонетки; 12 - труба;
13 — камера; 14 — насос.
Полученный бардяной уголь, содержащий некоторое количество органических
веществ, выгружается из печи скребками конвейера 10 и на вагонетках
11 отвозится в камеры 13 для дожигания. В камере уголь
остается около 2 недель, продолжая медленно гореть. После этого остаток,
состоящий из минеральных элементов барды, направляется на дальнейшую
переработку.
На каждые 1000 дал производимого в сутки спирта получается около 1
т бардяного угля с содержанием КзС03 до 60%.
Этот метод несложен, устраняет необходимость в полях фильтрации и
предохраняет водоемы от засорения их бардой.
Однако при этом методе не используется органическая часть барды и из нее
не извлекаются кормовые дрожжи. Поэтому такой метод нельзя признать
рациональным.
На некоторых спиртовых заводах США и других стран, перерабатывающих
мелассу, процесс перегонки совмещен с упариванием. Освобожденная от спирта
бражка упаривается до 75% сухих веществ. Для этого бражка подается на
четырехкорпусную выпарку, из второго корпуса которой конденсат, содержащий
весь отогнанный спирт, направляется на обычного типа ректификационный
аппарат непрерывного действия, а барда получается в виде концентрата.
Комплексная утилизация барды.
В отечественной и зарубежной практике
утилизация мелассовой барды организована в основном по двум схемам:
минерализация содержащихся в барде органических соединений и извлечение
минеральных и органических соединений.
За последние 10 лет за рубежом практикуют главным образом извлечение из
барды органических соединений.
В СССР на наиболее крупных мелассовых спиртовых заводах (Лохвицком,
Андрушевском), оборудованных уникальными установками по упариванию барды и
сжиганию ее в топках энергетических паровых котлов, проведены работы по
комплексной переработке отходов производства, в том числе барды.
На Лохвицком спиртовом комбинате организована комплексная утилизация
отходов при переработке мелассы на спирт по следующей схеме.
Из зрелой бражки перед сгонкой сепарированием получают 17—18 т
хлебопекарных дрожжей в сутки (см. стр. 115); завод выпускает ежедневно 11
—12 г жидкой углекислоты; жидкую барду упаривают до концентрации 75% сухих
веществ (см. стр. 146). Из упаренной барды дистилляцией ивлекают глицерин
(1 —1,2 т/сутки), а остаток барды сжигают и получают золу—
углекислый калий и соду (см. стр. 147). Стоимость утилизируемых отходов
(дрожжей, углекислого газа, глицерина и энергетического пара) составляет
29% от стоимости основной продукции (спирта, эфиро-альдегидной фракции и
сивушного масла). Таким образом, при комплексной утилизации мелассной
барды более полно используется ее органическая часть с получением
значительного количества энергии.
На этом заводе работают также установки по получению из барды бетаина и
глутаминовой кислоты.
В 1961 г. до 25% барды использовалось на выращивание кормовых дрожжей. С
пуском глутаминового цеха все количество получаемой барды будет полностью
утилизировано.
На Андрушевском спиртовом заводе освоено получение пекарских дрожжей,
упаривание и сжигание барды и получение бардяной золы.
На Мало-Висковском спиртовом заводе отходы производства используются для
выработки жидкой пищевой углекислоты, пекарских и кормовых дрожжей.
Проведенные в УкрНИИСПе (П. В. Рудницкий) исследования показали, что
наиболее перспективными являются следующие схемы (А и Б) комплексной
переработки мелассовой барды.
По схеме А из бражки выделяются хлебопекарные дрожжи, а из барды
вырабатываются: глутаминовая кислота (или глутамат натрия), бетаин
солянокислый (или бетаин свободный) и хлористые соли. Последние выделяются
из маточного бардяного раствора после извлечения из него азотистых
соединений и применяются в виде удобрительных туков.
Хлористые соли смешивают с сухим фильтрпрессным шламом, в результате чего
получают удобрительные туки следующего состава: 44,4% хлористого калия,
30,3% хлористого натрия, 9,3% сульфата калия и 16% хлористого кальция.
Такой удобрительный тук, содержащий также микроэлементы, представляет
особую ценность для культуры сахарной свеклы. Себестоимость 1 тонны этого удобрительного тука 8 руб. 53 коп., а калийные удобрения, выпускаемые химической промышленностью, стоят 12,5 руб. за 1 тонну.
По схеме Б из бражки выделяются хлебопекарные дрожжи, а на барде
выращивают сухие кормовые витаминизированные дрожжи. Вторичную барду
упаривают и сжигают для получения поташа, соды кальцинированной, сульфата
и хлористого калия. Такой тип предприятия рационален уже при
производительности спиртового завода в 3000 дал спирта в сутки и более.
Как показывают расчеты, чистая прибыль при переработке 1 тонны мелассы
по схеме А составляет 201,4 руб., а по схеме Б — 125,5 руб.
Следует отметить, что при переработке мелассы в сепарационных цехах
сахарных заводов с последующим извлечением из сепарационных щелоков
глутаминовой кислоты, бетаина, кормовых дрожжей и калийных солей (см. гл.
I), суммарная стоимость извлекаемых из 1 т мелассы веществ
определяется в 126,6 руб., что на 59% ниже возможного выхода продуктов при
аналогичной переработке отходов мелассы в спиртовом производстве.
На крупнейшем предприятии ГДР, перерабатывающем мелассу, — Герунгсхеми в Дессау организована комплексная переработка мелассы
с получением, помимо спирта и углекислоты (жидкой и твердой), следующих
продуктов:
1) цианистых продуктов — цианистый натрий и синильная кислота;
2) соединений бария — углекислый, азотнокислый, хлористый и гидрат окиси
бария;
3) бетаина и глутаминовой кислоты;
4) удобрений — щелочной фосфат, уголь-фосфат, сульфат аммония;
5) кормовых средств — сушеные кормовые дрожжи;
6) газов (сероводорода, метана и др.).
Схема комплексной переработки мелассы следующая.
На брагоректификационные аппараты поступает бражка, содержащая дрожжи.
Барда, содержащая после выхода из аппарата мертвые дрожжевые клетки,
поступает в сепараторное отделение. Отделенные на сепараторах дрожжи
высушивают на двухвальцовых контактных паровых сушилках.
Часть барды после сепарации направляют в бродильную батарею на сбраживание
непрерывным методом дрожжевыми грибками Торула. Выход сухих кормовых
дрожжей составляет 12 кг/м3 барды.
Основную часть барды после сепарации дрожжей нейтрализуют содой и
упаривают: вначале в трехкорпусной выпарке, работающей под вакуумом, с
аппаратами вертикального типа и циркуляционной трубой. После сгущения
барда поступает на однокорпусную выпарку, состоящую из испарителя и
четырех трубчатых выносных кипятильников, где упаривается до содержания
78% сухих веществ. На этих установках получают в сутки около
110 тонн упаренной барды, которую затем
коксуют и вырабатывают брикеты кристаллического цианистого натрия.
Углекислый барий получают из шпата, содержащего сернокислый барий, и
углекислого газа, выделяющегося при брожении. Дробленый шпат смешивают с
дробленым углем или коксом и обжигают во вращающихся трубчатых печах.
Полученный при обжиге сернистый барий выщелачивают водой, раствор
осветляют в декантаторах и сатурируют углекислым газом.
Раствор, содержащий углекислый барий в виде кристаллов, фильтруют на
вакуум-фильтрах и отфильтрованную соль высушивают.
Бардяной уголь (кокс), полученный при коксовании барды, смешивают с
суперфосфатом, дробят и обжигают во вращающихся печах. Спекшуюся массу
дробят на мельницах и применяют в качестве удобрения.
На всех чехословацких мелассовых спиртовых заводах барда по выходе из
бражной колонны упаривается на непрерывно действующих трехкорпусных
выпарках, после чего поступает на концентратор, который доводит содержание
сухих веществ в ней до 75%. Барда в таком виде в железнодорожных цистернах
отправляется на химический завод для переработки на бардяной уголь и
химические продукты.
Из 1 тонны барды (75% сухих веществ) получается примерно 250 кг
бардяного угля и 615 м3 газа, который после выделения из него
сажи используется для подогрева барды.
Газ, освобожденный от сажи, подвергается ступенчатому охлаждению и
обработке раствором серной кислоты. Из 1 тонны упаренной барды получают 39
кг сажи, 60 кг сернокислого аммония и 38 кг цианистых
соединений.
Бардяной уголь перерабатывается на поташ по следующей схеме. Бардяной
уголь измельчают на молотковой дробилке и при дроблении к нему добавляют 1
% извести по весу угля, после чего смесь поступает вместе с водой в
разварник. Смесь концентрацией 50,6—54,3% (по сахарометру) варится при
атмосферном давлении и температуре 100°С, после чего спускается в
отстойник для осаждения нерастворимой части.
Жидкая часть фильтруется на фильтр-прессах или барабанных вакуум-фильтрах
и поступает для упаривания на выпарную установку системы Роберта для
упаривания до 75,8% сухих веществ. Выпадающий при этом в осадок
сернокислый калий отделяется от жидкой фазы на центрифугах.
Отделенная жидкость упаривается в выпарном аппарате до концентрации 90,4%
(по сахарометру). Выпавший углекислый натрий разбавляется водой,
подогревается и отделяется на центрифугах, а раствор отстаивается и
охлаждается до температуры 35 °С, в результате чего из него выпадает соль
— хлористый калий. После отделения хлористого калия жидкость поступает на
ту же периодическую выпарку и упаривается до удельного веса 1,60. При
выпаривании выпадает остальная часть хлористого калия. При охлаждении
раствора не ниже чем до 35 °С выпадает осадок КNаСОз,
а при охлаждении до 1 °С получается так называемая ледяная щелочь, которая
упаривается затем до удельного веса 1,68—1,72.
После медленного охлаждения упаренного раствора в течение 12 часов до
температуры 84°С происходит кристаллизация гидрата углекислого калия,
который затем отделяется на центрифугах. Кристаллический порошок сушат в
паровых барабанных сушилках и упаковывают в металлические бочки. В этом
порошке содержится 83,5% углекислого калия.
На ряде спиртовых заводов поташ поступает на печи, где при высокой
температуре освобождается от воды и содержание в нем К2СОз
повышается до 95—96%.
В Польской Народной Республике проведены опыты по получению поташа
непосредственно из мелассовой барды с применением ионообменников вместо
сжигания барды. Для обессоливания был применен польский катионит К512 в
колонке, работающей в аммониевом цикле. После регенерации катеонита (МН4)2СО3
получен фильтрат, содержащий К2СО3,
некоторое количество Мg2СО3
и избыток карбоната аммония (последний выделяют при сгущении фильтрата и
используют повторно).
При подщелачивании обессоленной барды Са(ОН)2 все количество
карбоната аммония возвращают в процесс. Единственным реактивом,
расходуемым в большом количестве, является известковое молоко. В
результате ионообмена большая часть (80%) поташа получается с чистотой
95%. Остальная часть (20%) имеет чистоту 80%.
Использование мелассовой барды на корм животным.
Применение на корм свежей барды. Как указано выше, кормовая ценность
мелассовой барды составляет 0,061 единиц на 1 кг, что более чем на
40% выше кормовой ценности картофельной барды. Мелассовая барда отличается
высоким содержанием амидов и минеральных солей.
В течение длительного времени считалось, что мелассовая барда непригодна
для откорма животных. В литературе отмечалось, что вследствие наличия в
барде большого количества калийных солей у животных при кормлении бардой
наблюдаются тяжелые заболевания желудочно-кишечного тракта, часто
сопровождающиеся кровавым поносом; барда не отличается хорошими вкусовыми
качествами и неохотно поедается скотом.
Новейшими исследованиями Украинского института животноводства Полесья и
Лесостепи, Всесоюзного научно-исследовательского института мясной
промышленности, а также опытами Главскотооткорма по откорму скота
мелассовой бардой спиртовых заводов, применяющих серную кислоту,
установлена возможность скармливания животным мелассовой барды. В опытах с
крупным рогатым скотом на каждую голову средним живым весом 350 кг
скармливали до 40 кг и более мелассовой барды в сутки (табл. 21).
Таблица 21
Состав рациона кормов на 1 голову в сутки
Место проведения опытов |
Мелассовая барда в л |
Сено |
Солома |
Концентрированные корма |
Жом |
Меласса |
Костяная мука |
Соль |
Мел |
Суточный привес |
Примечание |
в кг |
в г |
Дублянский спиртовой завод
(Украинский институт животноводства) |
40 |
2,4 |
1,8 |
1,43 |
|
|
|
60 |
40 |
600 |
|
Ивашковский откормочный совхоз
(ВНИИМГР)
|
25 сепарир. |
|
|
|
|
|
|
|
|
|
|
I фракц. |
2,48 |
2,18 |
1,93 |
— |
1,06 |
— |
— |
— |
721 |
|
25 II фракц. |
2,47 |
2,18 |
1,97 |
— |
1,06 |
— |
— |
— |
728 |
|
36 |
2,47 |
2,18 |
1,95 |
— |
1,07 |
— • |
— |
— |
974 |
|
Будымский откормочный совхоз |
50—60 |
|
2,5—3,0 |
1,7 |
Сухой 1 — 1,5 |
_ |
_ |
60 |
40 |
709 |
Откормлено несколько тысяч
голов (1954 г.) |
Шевченковский откормочный
пункт (Киевская обл.) |
30 |
_ |
5,5 |
1,0 |
Кислый 10 |
2,0 |
20 |
40 |
__ |
667 |
|
Барский межколхозный
откормочный пункт |
35—40 |
_ |
6,8 |
|
Свежий 25-30 |
_ |
_ |
70—90 |
70-90 |
470 |
От кормлено 1 1 56 голов
молодняка крупного рогатого скота без концентрированных кормов |
Всесоюзный научно-исследовательский институт мясной промышленности,
Удельный вес мелассной барды по питательности достигал в общем рационе
40%.
Исследованиями подтверждено, что при скармливании свежей мелассной барды
крупному рогатому скоту, а также молодняку получаются хорошие результаты и
никаких вредных последствий не наблюдается. Мелассной бардой не
рекомендуется кормить стельных коров, свиней и лошадей. Консервированная
мелассовая барда для скармливания непригодна.
На основе этих исследований утвержден примерный рацион питания скота с
применением 45—50 кг мелассной барды на 1 голову в сутки (табл.
22).
Таблица
22
Примерный рацион питания для
крупного рогатого скота, утвержденный Министерством сельского хозяйства
УССР
Живой вес |
Мелассная барда в кг |
Сено |
Солома |
Дерть кукурузная |
Свекла кормовая |
Соль в г |
Мел |
400—500 |
50 |
2,0 |
3,0 |
2,0 |
10 |
100 |
80 |
220—260 |
45 |
2,5 |
2,0 |
2,0 |
5 |
60 |
50 |
Расчеты показывают, что мелассовый спиртовой завод производительностью
3000 дкл спирта в сутки получает такое количество барды, которым
можно откармливать в смеси с другими кормами 975 голов крупного рогатого
скота и получать ежесуточный прирост мяса в живом весе около 2,3 т.
Из сказанного вытекает, что использование мелассовой барды на корм
заслуживает широкого применения, особенно на заводах небольшой и средней
мощности.
При средних мелассных спиртовых заводах производительностью 2500—3000
дкл спирта в сутки наиболее целесообразно организовать межколхозные
откормочные пункты для откорма скота бардой, что дало бы возможность
механизировать транспортировку свежей барды непосредственно к месту
потребления.
На мелассных спиртовых заводах следует применять для подкисления среды
вместо серной кислоты соляную, а вместо пентахлорфенолята натрия как
антисептика использовать формалин или хлорную известь, что значительно
повысит кормовую ценность мелассовой барды.
Барду можно использовать для запаривания грубого корма скоту, что также
позволит использовать содержащиеся в ней питательные вещества.
Силосование кормов с применением мелассной барды. При силосовании кормов для проведения направленного молочнокислого закисания, а также для обогащения силоса белками и другими питательными веществами рекомендуется в процессе
закладки силоса добавлять свежую, охлажденную до температуры 30 °С,
мелассовую барду. В первую порцию барды, предназначенной для силосования,
через 20—24 ч при температуре 50—52 °С задают чистую культуру
молочнокислых бактерий (0,5—1 % от количества задаваемой барды). После
размножения в барде молочнокислых бактерий (за счет сахара барды) ее
охлаждают до 30—32 °С и выкачивают в силосные траншеи или силосные башни.
Затем в силосную массу добавляют барду с температурой 30 °С для
поддержания общей влажности в силосуемых кормах 60—75%.
Добавляемая в силосный корм барда вытесняет воздух из силосуемой массы,
что устраняет возможность развития в ней гнилостных бактерий.
Использование на корм сушен ой барды. Вторичная барда после выращивания и
сепарации кормовых дрожжей содержит 7,5—8,5% сухих веществ. Из 1 тонны
исходной барды получается 850 кг вторичной барды. Эту барду можно
использовать на корм как в упаренном, так и в сухом виде.
При опытном скармливании скоту упаренной барды получены положительные
результаты.
В Лодзинском Политехническом институте (Польша) разработан метод
обогащения сгущенной мелассовой барды аммонием или кальцием. При помощи
ионообменников в барду вместо калия вводится аммонийная группа или ионы
кальция. В результате из барды частично удаляется калий, значительное
содержание которого в барде нежелательно при скармливании скоту, и
получается чистый поташ (без примеси хлоридов или сульфатов).
Сгущенная до 65% сухих веществ мелассовая барда, лишенная калия и
обогащенная аммонием или кальцием, является ценным кормом. Такая барда
содержит в пересчете на сухое вещество 5% натурального азота и 4% азота,
связанного ионной связью. В 100 кг этой барды содержится 1,3 кг
усвояемого азота, что соответствует 8 кг белка, и около 5 кг
СаО, а крахмальный эквивалент ее равен 30.
В Китайской Народной Республике мелассовую барду продают крестьянам,
которые используют ее как удобрение и для кормления рыбы в прудах.
Мелассовую барду также используют на корм, смешивая ее с
поглощающей жидкость багассой; полученное кормовое средство применяют в
окрестных хозяйствах.
Получение глутамата натрия из мелассы
|