Для производства ферментного препарата Глюкаваморин Гх-466 в рамках собственного производства на спиртовом заводе применяется непрерывный глубинный способ выращивания продуцента Aspergilius awamori - 466 на жидкой питательной среде, основу которой составляет фугат послеспиртовой барды, с интенсивной аэрацией стерильным воздухом.
Технологический
процесс производства фермента Глюкаваморин Гх-466 состоит из следующих стадий:
-
приготовление посевного материала в лаборатории;
-
приготовление жидкой посевной культуры;
-
приготовление питательной среды для ферментации;
-
ферментация.
Приготовление посевного материала. Споровый посевной материал гриба Aspergilius awamori - 466 готовят в лаборатории в пробирках на агаризованной питательной среде, имеющей следующий состав (в %):
-
Глюкоза
2,0
-
Нитрат натрия 0,91
-
Хлорид калия 0,05
-
Сульфат магния 0,05
-
Дигидроортофосфат 0,10
-
Сульфат железа
(Ре2+)
0,001
-
Вода дистиллированная 96,84
Среду стерилизуют в течение 40 минут при давлении 0,1
МПа.
Культура гриба
рассевается на скошенную в пробирках среду и выращивается в течение 12 суток в
термостате при 25° С. Готовая культура должна иметь характерный для вида цвет и складчатую поверхность. Она используется для приготовления
жидкого посевного материала.
Приготовление жидкой посевной культуры фермента Глюкавоморин. Жидкая посевная культура готовится в
несколько стадий. По 3-х стадийной схеме на первой стадии готовят
питательную среду следующего состава (в %):
-
Кукурузная мука 5,0
-
Дрожжевой автолизат 0,5
-
Вода
94,5
Разбавленным раствором серной кислоты
рН среды доводят до 4,8.
Приготовленную среду разливают в качалочиые колбы на 500 мл по 300 мл в каждую
и стерилизуют при температуре 121—125°С в
течение 40—60 мин. После стерилизации среду охлаждают до 26° С и
засевают суспензией конидий, полученных при выращивании культуры на скошенной
агаризованной среде в пробирках. Колбы ставят на качалку. Выращивание проводят при температуре 24—26° С в течение 36—48 ч при частоте колебаний качалки
200—220 мин -1.
Через 36—48 ч (по заключению сменного
микробиолога) жидкую культуру передают на
вторую стадию.
Питательную среду для второй стадии готовят
аналогично первой стадии. После доведения рН до 4,8, стерилизации при
температуре 121—125° С в течение 40—60 мин и охлаждения до 26° С питательную
среду разливают в сосуды вместимостью 6 литров по 2,5 литров в каждый и засевают жидкой
посевной культурой первой стадии в количестве 10—12% к объему среды.
Выращивание проводят при температуре 24—26° С при частоте колебаний качалки
200—220 мин-1.
Выращенная жидкая посевная культура второй
стадии является посевным материалом при выращивании засевной культуры. Объем
посевной культуры должен составлять 0,5—1,0% к объему питательной среды в инокуляторе.
На третьей стадии жидкая посевная культура выращивается в производственных условиях в посевных
аппаратах — инокуляторах (рис.
1). Технологический цикл состоит из следующих операций: подготовка аппарата, приготовление и стерилизация питательной среды,
засев среды культурой, культивирование микроорганизмов.
Посевной аппарат 10 представляет
собой цилиндрический сосуд со сферическим
днищем и крышкой. Аппарат оборудован устройством для аэрации и перемешивания
(форсунки или барботеры, двухъярусная мешалка), подводом для пара,
посевным лючком, узлом для отбора проб, гильзой для термометра, штуцерами для
подачи питательной среды и спуска промывных вод, для манометра, подводом и
отводом воздуха, люком для мойки и осмотра аппарата и линией спуска готового
посевного материала. Корпус аппарата имеет рубашку для охлаждения. Каждый
аппарат снабжен индивидуальным воздушным фильтром.
Для строгого соблюдения
стерильных условий необходимо, чтобы на всех трубопроводах была установлена хорошо притертая арматура. Вентили целесообразно использовать
бессальниковые с мембраной из
термостойкой резины или пластмассы (фторопласт-4, полипропилен).
Арматура в работе должна быть под паровой защитой.
Подготовка посевного
аппарата к приему питательной среды производится следующим образом. Через открытую крышку люка ополаскивают
внутреннюю поверхность аппарата из
шланга водой. Затем осматривают аппарат, прокладки и проверяют работу
барботера или форсунки. Для этого в аппарат набирают воду до покрытия форсунки или барботера и подают в них воздух.
Аппарат после осмотра проверяют на
герметичность воздухом под давлением 0,07 МПа. С помощью мыльной пены,
нанесенной на места соединения (крышка, фланцы, смотровые стекла, сальники,
вентили и т. д.), паровые и материальные вентили проверяют на герметичность
паром. Если обнаружены пропуски воздуха или пара, а также снижение давления в
аппарате, устраняют обнаруженные дефекты и
снова проверяют аппарат на герметичность.
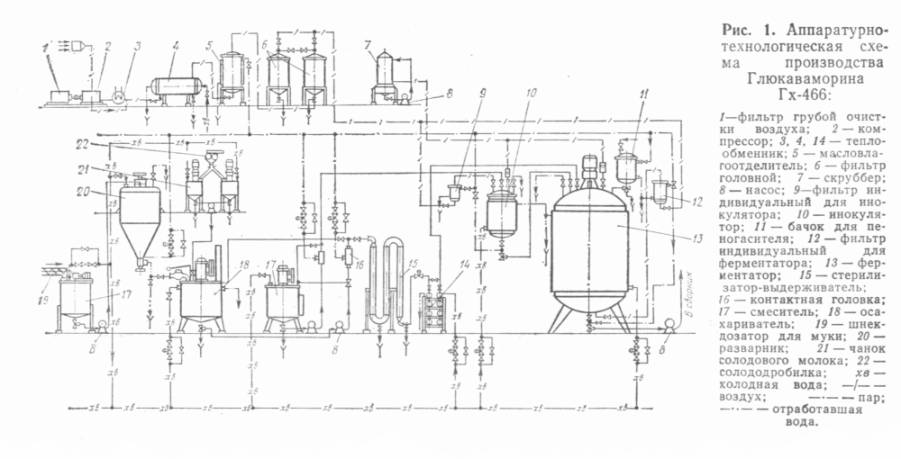
Давление в аппарате
должно выдерживаться без изменения в течение 30 мин.
Длительность
обработки посевного аппарата и проверки его на герметичность составляет 1,5—2,5
часа.
После проверки на
герметичность аппарат стерилизуют вместе с коммуникациями и индивидуальным
фильтром острым паром. Пар подается через фильтр, барботер или форсунку,
посевную и спускную линии. Началом стерилизации считается время достижения
температуры 126—132° С, стерилизация проводится в течение 1 ч при давлении
0,18—0,20 МПа.
Во время стерилизации аппарата острым паром стерилизуются пробоотборник, барботер или форсунка,
питательная спускная и выхлопная линии. Избыточное давление в аппарате во время стерилизации сбрасывается через выхлопную линию, конденсат сливается.
По окончании стерилизации подача пара на фильтр прекращается. Фильтр отдувается стерильным
горячим воздухом.
Перед поступлением питательной среды в аппарат открывают пар на аэрирующее устройство и включают
насос подачи питательной среды. В качестве питательной среды используется кукурузное сусло, разбавленное в смесителе 17 водой до содержания сухих
веществ 6% по сахарометру. Для разбавления в смеситель набирают воду и при
постоянной работе мешалки из осахаривателя 18 вносят сусло. Соотношение сусла
и воды должно быть равным 1:2. После тщательного перемешивания питательную
среду нагревают в контактной головке 16 до 85°С путем многократного
перекачивания насосом. Подогретую среду перекачивают в подготовленный посевной
аппарат. Для предотвращения ценообразования в среду перед подогревом добавляют
подсолнечное масло из расчета 0,10—0,15%.
В посевном аппарате
10 среда сначала подогревается до 100°С острым паром через форсунку, линию
передавливания и нижний спускной штуцер при открытой выхлопной воздушной линии.
Затем вентиль на выхлопной линии закрывается и температура среды поднимается
до 121—123° С (давление 0,10—0,15 МПа). При этой температуре среда
выдерживается в течение 60 мин. По окончании стерилизации прекращается подача
пара.
Постепенно, во
избежание вскипания среды, открывается вентиль на выхлопной линии, давление а
аппарате медленно снижается до 0,03—0,05 МПа. Затем в аппарат постепенно
подается стерильный воздух для поддержания в нем избыточного давления 0,02—0,03
МПа, а в рубашку аппарата поступает холодная вода.
После охлаждения
массы до 27 С производится засев среды
посевной культурой, полученной на второй стадии, в количестве 0,5—1,0%.
Засев ведется через посевной лючок с соблюдением условий стерильности при
минимальном движении окружающего воздуха.
Перед засевом
прекращается подача воздуха в аппарат и одновременно закрывается вентиль на
выхлопной линии. Вокруг посевного лючка зажигается факел из ватных тампонов,
смоченных спиртом, лючок открывается и через зону огня вносится посевная культура
из колб. После этого лючок быстро закрывается, включается подача воздуха и
приоткрывается вентиль на выхлопной линии. В аппарате устанавливается
избыточное давление 0,02—0,03 МПа.
Интенсивность аэрации
среды контролируется через смотровое стекло с учетом показаний расходомера.
Показатели питательной среды должны быть в пределах:
Концентрация сухих веществ, % 5,5—6,0
Температура, °С 27—28
Процесс выращивания посевного материала должен
проходить при следующих условиях:
Давление в аппарате в процессе роста, МПа 0,02—0,03
Расход воздуха на аэрирование 1 м3 питательной среды, м3/ч 16
Способ перемешивания Двухъярусной турбинной
мешалкой, ω = 350 мин-1
Температура воздуха на входе в аппарат, °С 35—40
Продолжительность выращивания, ч 24
Спускная линия, пробоотборный узел и нижний спускной
вентиль в течение всего периода ферментации должны находиться под паром.
Температура в процессе ферментации поддерживается автоматически путем подачи
холодной и теплой воды в рубашку.
В готовой посевной культуре не должно быть посторонней
микрофлоры; мицелий должен представлять собой длинные ветвистые гифы с
однородной протоплазмой, биомасса — средней густоты и равномерно распределенная
в объеме пробы.
Производственный цикл посевного аппарата складывается
из следующих операций (в ч):
Проверка на герметичность 0,5—1,0
Проверка давления и стерилизация аппарата 2,5
Загрузка средой 0,5
Подъем давления и стерилизация питательной среды 1,5
Охлаждение и засев питательной среды 2,0—3,0
Выращивание посевной культуры 18—24
Передача посевной культуры в ферментатор 0,5
Общая продолжительность цикла 25—34
Через 12 часов от начала выращивания и перед посевом в ферментатор с соблюдением условий стерильности
отбираются пробы из инокулятора для определения рН, концентрации сухих веществ,
зарязненности посторонней микрофлорой. При обнаружении посторонней микрофлоры
культуру из аппарата сливают и посевную культуру готовят заново. Перед сливом
инфицированную культуру стерилизуют в течение 2 часов паром при температуре
126—132° С и давлении 0,18—0,2 МПа и подают на биологическую очистку.
Допускается хранение посевной культуры в течение
нескольких часов в инокуляторе в охлажденном виде (12 — 15°С). При этом в
рубашку инокулятора подается вода, аэрация сохраняется постоянно. Количество выделяемого
биологического тепла в процессе роста культуры составляет 5000—6300 кДж/час на 1
м3.
Производственное выращивание культуры. Производство и выращивание глубинной культуры Asp. awamori-466
в спиртоаом производстве осуществляется в ферментаторе из нержавеющей стали в стерильных
условиях при постоянном перемешивании и аэрировании среды. Технологический
цикл производства ферментного препарата состоит из следующих операций: подготовка ферментатора к приему
питательной среды, приготовление питательной среды, стерилизация питательной
среды, охлаждение и засев питательной среды в ферментаторе, ферментация.
Ферментатор, в котором
выращивается глубинная культура, снабжен рубашкой для обогрева и охлаждения,
аэрирующим устройством, подводами для пара, посевной и спускной линиями, гильзой
для манометра и термометра, узлом отбора проб, пеногасительным бачком и
индивидуальным воздушным фильтром.
Подготовка ферментатора к приему питательной среды производится следующим
образом. После освобождения от культуральной жидкости ферментатор моют водой из
шланга, осматривают снаружи и внутри. Затем аппарат вместе с прилегающими к
нему коммуникациями проверяют на герметичность воздухом при давлении 0,07 МПа с
помощью мыльной пены.
При полной герметизации
аппарата и прилегающих коммуникаций приступают к их одновременной
стерилизации. Для стерилизации ферментатора острый пар подают на аэратор,
линию подачи питательной среды, спускную линию и линию передавливания посевного
материала. Нагрев аппарат, закрывают вентиль на выхлопной воздушной линии и
поднимают давление. Стерилизацию ведут при температуре 120 — 125°С, давлении 0,2
МПа в течение 1 часа. Избыточное давление сбрасывается через выхлопной вентиль.
По окончании стерилизации
отключают от ферментатора 13 пеногасительный бачок и индивидуальный воздушный
фильтр и охлаждают аппарат до 50 — 55°С. Поддерживая давление в аппарате
0,02—0,03 МПа, сливают образовавшийся конденсат и приступают к приему
стерильной и охлажденной до 27° С питательной среды.
Питательную среду готовят, используя кукурузное сусло с концентрацией сухих
веществ 18—20%, которое получают по следующей схеме: кукурузную муку через
порционные автоматические весы загружают в смеситель 17, в который
одновременно и при постоянной работе мешалки поступает вода с температурой не
более 45°С. Соотношение муки и воды 1 : (2,5—3,0).
Полученную массу насосом
перекачивают в варочный аппарат, работающий под давлением. массу в аппарате
нагревают острым паром, который вводят снизу. Разваривание производится при температуре
148—154° С и давлении 0,36—0,44 МПа 15—20 мин.
Разваривать муку можно как в
аппаратах периодического действия, так и по непрерывному способу в варочном
аппарате трубчатого типа, к которому подведен пар давлением не менее 0,5 МПа.
Разваренная масса поступает в
осахариватель 18, оборудованный змеевиком для охлаждения. Перед выдуванием
массы в осахариватель набирают воду в количестве 5% к объему массы.
Разваренную массу
охлаждают до 63° С, затем осахаривают солодовым молоком, которое получают
смешиванием в солодовых чанках измельченного на солододробилке солода и воды.
Соотношение солода и воды 1 : (6—8). Продолжительность осахаривания при
температуре 58—60˚ С составляет 30 мин.
Полученное сусло с концентрацией
сухих веществ 18—20% и рН 5,3—5,6 насосом подается на контактную головку 16,
прокачивается через нее, прогреваясь острым паром до 85° С, и подастся в
стерилизатор 15.
Стерилизация питательной среды осуществляется на установке, включающей контактную
головку, трубчатый выдерживатсль и теплообменник 14. Перед стерилизацией среды
систему проверяют на герметичность паром под давлением 0,20— 0,25 МПа. При
обнаружении пропусков пара снижают давление до нуля, устраняют дефекты и вновь
проверяют систему на герметичность. При полной герметизации систему
стерилизуют острым паром в течение 30—40 мин при давлении 0,2—0,25 МПа. По
окончании стерилизации системы приступают к стерилизации среды. Питательная
среда температурой 75 — 80°С плунжерным насосом подается через контактную
головку, где нагревается до температуры 120 — 125° С, в трубчатый выдерживатель-стерилизатор 15, где выдерживается 30—40 мин, затем охлаждается в
теплообменнике 14 до 35°С и поступает в ферментатор. При работе теплообменника
обводная линия, вентили подачи воды и спуска среды должны быть под паровой
защитой. При отсутствии теплообменника питательная среда непосредственно из
выдсрживателя поступает в ферментатор. В процессе его заполнения в аппарате
поддерживают давление 0,10—0,12 МПа. Острый пар в это время подается только
через систему аэрации. Охлаждается среда непосредственно в ферментаторе.
После заполнения
ферментатора всю систему освобождают от среды, прокачивают водой для удаления
взвешенных частиц питательной среды и стерилизуют острым паром в течение 30—40
мин при давлении 0,20—0,25 МПа. Освобождение и прокачка системы осуществляются
на смеситель. Расход воды при этом должен составлять 2—3 объема системы.
Засев среды в ферментаторе осуществляется по линии передавливания,
предварительно простерилизованной от посевного аппарата до ферментатора острым
паром в течение 1 часа. Перед засевом из ферментатора отбирают пробы среды через
пробоотборник на микробиологический высев (на МПБ и МПА) и биохимический
анализ.
Для засева закрывают вентиль
на выходной воздушной линии у посевного аппарата и поднимают давление до
0,06—0,08 МПа, а в ферментаторе оставляют давление 0,02—0,03 МПа. После этого
открывают вентиль на линии передавливания у посевного аппарата и ферментатора и
за счет разности давления посевную культуру передавливают в ферментатор.
Закрывают вентиль на линии передавливания, включают мешалку и начинают процесс
выращивания культуры в ферментаторе. По окончании засева линию передавливания
пропаривают. Количество посевного материала составляет 3% к объему питательной
среды в ферментаторе.
Процесс ферментации протекает при следующих
условиях:
Пробоотборники и нижняя
сливная линия с момента загрузки среды и в процессе ферментации находятся под
паром. Продолжительность ферментации 120—160 часов (до окончания накопления
глюкоамилазы).
Для микробиологического и
биохимического контроля развития культуры с соблюдением всех условий
стерильности отбираются пробы из ферментатора через 72 ч после посева, а затем
через каждые сутки роста. В пробах определяются глюкоамилазная активность,
рН, концентрация сухих веществ, состояние культуры и отсутствие посторонней
микрофлоры при микроскопировании.
В готовой культуре перед
сдачей в спиртовое производство для осахаривания определяется содержание общих
и растворимых углеводов.
Готовая культура должна
удовлетворять следующим требованиям:
Концентрация сухих веществ в фильтрате культуры, % 8—10
рН 3,0—3,5
Наличие посторонней микрофлоры Отсутствует
Примечание.
В случае развития инфекции ферментатор стерилизуется в течение 2 ч при
126—132° С и давлении 0,18— 0,20 МПа, а культура подается на биологическую
очистку.
Готовая культура Аsр.
аwamory-466 насосом подается в предварительно стерилизованные сборники,
снабженные системой охлаждения (охлаждение культуры идет до 8—12°С),
расположенные в спиртовом производстве.
Ниже приведен производственный цикл
ферментатора (в ч):
Мойка и осмотр 1,5
Проверка на герметичность
1,0
Подъем давления 0,5
Стерилизация 1,0
Заполнение питательной средой 4,0
Охлаждение среды 4,0*
Ферментация 120—168
Передача культуры в расходные емкости для осахаривания крахмала или на фильтрацию 1,0**
Общая продолжительность цикла
129—177
* Для ферментаторов вместимостью 30 м3. При отсутствии теплообменника производственный цикл ферментатора увеличивается на 4 часа.
** Зависит от вместимости сборников и
производительности насосов.
Для обеспечения стерильных условий при культивировании
необходимо кроме надежной стерилизации среды и аппаратуры строго следить за
стерильностью подаваемого на аэрацию воздуха.
Отделение от воздуха механических примесей и
микроорганизмов осуществляется через систему тройной очистки. Для очистки воздуха
от механических примесей перед компрессором устанавливают висциновый фильтр /.
Для подачи воздуха применяются компрессоры 2.
Отделение влаги и масла от воздуха после компрессора
производится во влагоотделителе 5.
В теплообменнике 4 воздух подогревается до температуры
60— 80° С в зависимости от температуры наружного воздуха и температуры в
помещении. Очистка воздуха после теплообменника от посторонней микрофлоры
происходит в общем (головном) фильтре 6, заполненном базальтовым волокном.
После головного фильтра воздух подается в коллектор, а затем дополнительно
очищается на индивидуальных фильтрах 9 н 12 с базальтовым волокном, установленных
соответственно перед каждым инокулятором и ферментатором.
Для бесперебойного снабжения установки стерильным
воздухом необходимо наличие двух головных фильтров. Перебивку головного фильтра
проводят 1—2 раза в год. После перебивки головной фильтр стерилизуют острым
паром при 130—150° С в течение 4—6ч, затем отдувают горячим воздухом с
температурой 110—114° С до полного удаления влаги. Индивидуальные фильтры
перезаряжают через 3—4 ферментации. В случае переброса среды в фильтр или
нестернльности ферментации производится его внеочередная перебивка.
Индивидуальные фильтры стерилизуют вместе с посевным
аппаратом и ферментатором острым паром в течение 2 ч при давлении 0,18—0,20
МПа. Для удалении влаги из фильтров их продувают горячим воздухом.
Контроль за перебросами питательной среды в фильтры
ведется постоянно, для этого вентили отбора проб воздуха на фильтрах должны
периодически открываться.
Необходимо систематически вести контроль за
стерильностью поступающего на аэрацию воздуха. Способ проверки воздуха
заключается в следующем. Колбу вместимостью 0,5—1,0 л со стерильным
мясо-пептонным бульоном (100—150 мл) стерильно присоединяют к специальному
пробному кранику воздуховода и начинают отбор воздуха с продуванием его через
мясо-пептонный бульон. Воздух продувают 10—12 ч, при этом бульон не должен
сильно пениться. По истечении этого времени плотно зажимают шланги выхода и
входа воздуха, закрывают пробный краник воздуховода, отсоединяют колбу и
выдерживают ее в термостате при 37±0,5˚ С в течение 48 ч.
При наличии даже небольшого помутнения отмечают нестерильность
воздуха.
В процессе производства глубинной культуры по
различным причинам могут произойти нарушения технологического процесса.
Возможные способы устранения неполадок указаны в табл. 30.
В табл. 31 представлены нормативные величины затрат
времени на проведение операций при производстве препарата Глюкапаморин Гх-466.
Технологический
процесс производства Амиломезентерина Гх-467
Для получения препарата
Амиломезентерин Гх-407 применяется также глубинный способ выращивания
продуцента Вас. mesentericus ПБ-467 на жидкой питательной
среде с интенсивной аэрацией.
Процесс получения культуры
включает приготовление посевного материала и выращивание производственной
культуры Вас. mesentericus ПБ-467.
Приготовление посевного материала. Ампулы с хранящейся в песке культурой Вас. mesentericus ПБ-467 поступают на завод из
ВНИИПрБ. На каждой ампуле должна быть этикетка с названием культуры, датой
начала хранения и подписью микробиолога.
Д ля оживления культуры
используют мясо-пептонный бульон (МПБ), который разливают в конические колбы
объемом 750—1000 мл в количестве 75—100 мл. Колбы закрывают ватными пробками и
стерилизуют при температуре 120° С в течение 30 мин, затем выдерживают в
термостате при температуре 37±0,5°С в течение суток.
В приготовленный таким образом
МПБ в стерильном боксе переносят стерильно содержимое ампулы с культурой.
Выращивание осуществляется в термостате при температуре 40±0,5° С в течение
40—48 ч. На поверхности бульона образуется белая складчатая пленка. Бульон
должен оставаться прозрачным, однако возможно слабое хлопьевидное помутнение.
Оживленная на МПБ культура
может храниться при 4—6° С в течение 10 дней, при 20° С — не более 3 сут.
Для проверки культуры на
чистоту используют мясо-пептонный агар (МПА). Стерильный МПА разливают в стерильные
чашки Петри и помещают их на сутки в термостат при температуре 37± ±0,5° С.
Убедившись в стерильности МПА в чашках, его используют для работы.
Оживленную культуру петлей
стерильно переносят в пробирку со стерильной дистиллированной водой, энергично
встряхивают 5— 10 мин и отбирают стерильной пипеткой 0,2—0,3 мл в чашку Петри,
размазывая среду стерильным1 шпателем по поверхности МПА.
Чашки со средой выдерживают
в термостате при температуре 40±0,5°С в течение 24—40 ч. На поверхности МПА
должны вырасти только колонии микроорганизмов, характерные для Вас. mesentericus ПБ-467. Присутствие другой микрофлоры
свидетельствует о нестерильности посуды или оживленной культуры. Такую культуру
нельзя использовать для производства. Колбы следует простерилизовать при температуре
127° С в течение 2 ч.
Посевной материал выращивают
поверхностным способом на жидких питательных средах. Посевным материалом для
ферментации может служить оживленная на МПБ культура, которая прошла проверку
на чистоту.
Для получения посевного материала
используется солодовое сусло с концентрацией СВ 8—12% и рН 7,3 (доводится
33%-ным раствором NaOH). Солодовое сусло разливают в конические колбы
объемом 750—1000 мл в количестве 75—100 мл, колбы закрывают ватными пробками и
стерилизуют в автоклаве при температуре 110° С, давлении 0,15 МПа в течение 30 мин. Затем
колбы помещают на сутки в термостат при температуре 37±0,5° С. Выдержанное
стерильное сусло должно быть прозрачным и не иметь на поверхности пленки
микроорганизмов.
Засев питательной среды
культурой Вас. mesentericus осуществляется
следующим образом. В стерильном боксе оживленную культуру петлей стерильно
переносят на поверхность питательной среды (для засева достаточно 1—2 петель).
Колбы с засевной средой не рекомендуется взбалтывать. Посевной материал
выращивается в термостате при температуре 40±0,5°С в течение 24 или 40 ч.
Культура на солодовом сусле вырастает в виде белой складчатой бархатистой
пленки.
Микробиологический контроль
посевного материала заключается в проверке его на чистоту и на отсутствие
бактериофага. Проверка посевного материала на чистоту проводится тем же
способом, что и проверка оживленной культуры. Результаты проверки должны удовлетворять
требованиям, предъявляемым к оживленной культуре.
Проверка на отсутствие бактериофага
производится следующим образом. Посевной материал петлей (1 раз) стерильно
переносят в пробирку со стерильной дистиллированной водой. Пробирку энергично
встряхивают в течение 5—10 мин, после чего из нее отбирают 0,2—0,3 мл среды и
переносят в чашку Петри с чистой культурой Вас. mesentericus на МПА. Испытуемый посевной
материал шпателем тщательно размазывают по всей поверхности. Инкубацию
культуры осуществляют в термостате при температуре 40±0,5°С в течение 24 ч.
После инкубации на чашках Петри с чистой культурой не должны выявляться фагоцитозные пятна, которые указывают на лизис бактерий бактериофагом.
Посевной материал,
проверенный на чистоту и отсутствие бактериофага, используется для засева питательной среды в производственном
ферментаторе. До засева посевной материал желательно не взбалтывать и
хранить при температуре 4-6° С.
Выращивание производственной культуры. Технологический цикл состоит из следующих
операций: подготовка ферментатора, приготовление и стерилизация питательной
среды, стерилизация пеногасителя, стерилизация воздуха, засев питательной среды
в ферментаторе, ферментация.
Подготовка ферментатора
осуществляется так же, как и при производстве Глюкаваморина Гх-466.
Выращивание культуры Вас. mesentericus ПБ-467 в производственных ферментаторах проводится на питательной среде
следующего состава (в %):
Кукурузный экстракт 1,0
Дигидроортофосфат калия (диаммонийфосфат) 0,9
Мел 0,2
Подсолнечное масло (пеногаситель) 0,05
Вода 91,85
Питательная среда готовится в смесителях с мешалками (см. рис. 1). В первом смесителе соли и водорастворимые компоненты смешиваются с водой. После размешивания смесь насосом
перекачивается во второй смеситель, в который задастся мука. После заваривания
муки рН среды доводят раствором NaOH до 7,3 и добавляют пеногаситель.
До подачи на стерилизацию питательная среда нагревается острым паром до 75—80°
С.
Стерилизация питательной
среды осуществляется на обычном установке непрерывной стерилизации, состоящей
из контактной головки, трубчатого выдерживателя и теплообменника для охлаждения
среды. Нагретая питательная среда центробежным насосом подается в греющую
колонку, где она подогревается острым паром (давление 0,4—0,5 МПа) до 132—136°
С, и затем в выдерживатель, где выдерживается при этой температуре в течение
25—30 мин. Из выдерживателя среда поступает в теплообменник, где охлаждается до
40—42° С. Для предотвращения проскоков нестерилизованной среды в теплообменник
первые ее порции возвращаются через байпас в смеситель.
Из теплообменника питательная
среда непрерывно отводится в предварительно подготовленный ферментатор. Во
время приема среды в ферментаторе поддерживается давление 0,02—0,03 МПа. В случае
сильного вспенивания во время загрузки или перед посевом среды в ферментатор
подается стерильный пеногаситель. Объем среды должен составлять 60—65% от
объема ферментатора. Если он меньше, то недостающий объем заменяют водой,
которую подают в ферментатор через систему стерилизации.
Подготовка воздуха производится по той же схеме, что и при производстве ферментного препарата Глюкаваморина Гх-466.
Питательная среда засевается в ферментатор через штуцер со строгим
соблюдением стерильности при минимальном движении воздуха в цехе. После
загрузки ферментатора через пробоотборник стерильно отбирают пробу среды на
проверку ее стерильности, а затем давление в ферментаторе снижают до нуля,
прекращают подачу воздуха и одновременно закрывают вентиль на выхлопной линии.
Вокруг штуцера, через который осуществляется посев, зажигают факел, открывают
штуцер и через зону огня вносят посевную культуру из колбы. После этого штуцер
быстро закрывают, включают подачу воздуха и приоткрывают вентиль на выхлопной
линии. В ферментаторе устанавливается избыточное давление 0,015—0,020 МПа.
Для засева питательной среды
в ферментаторе необходимо иметь 3—4 колбы с посевным материалом. Перед самым
посевом содержимое колб стерильно (в боксе) сливают в одну.
Процесс ферментации протекает
при температуре 40— 42°С, которая поддерживается автоматически путем подачи
теплой воды в рубашку аппарата. Аэрация среды стерильным воздухом и ее
перемешивание мешалкой (частота вращения 200—220 мин-1) производятся
непрерывно с момента окончания посева и до конца процесса ферментации. Расход
воздуха составляет 30—40 м3/ч па 1 м3 среды.
Пробоотборник и нижняя
сливная коммуникация должны находиться под паром, при вспенивании среды в
процессе ферментации добавляется стерильный пеногаситель.
Общая продолжительность ферментации составляет 30—40 часов.
В процессе ферментации
ведется строгий микробиологический и биохимический контроль за культурой. Для второго при соблюдении всех условий стерильности через каждые 6 часов отбирают пробы из ферментатора..
В норных двух пробах после засева определяют чистоту процесса ферментации и рН среды, который должен составлять 0,5—7,0.
После 12 часов роста культура под
микроскопом представляет собой отдельные пли соединенные в цепочки по 2—3 короткие
палочки. Через 18 часов роста, когда в среде уже нет крахмала, начинают контролировать
биосинтез а-амилазы. К 24 часу роста культура представляет собой отдельные палочки
размером 4—5 мкм в длину и 1 мкм в ширину, активность а-амилазы в этот период
должна составлять 15—20 ед./мл. К 30—36 часу роста это уже палочки со спорами,
встречаются мертвые клетки, более прозрачные и бледные при контрастирующей
фазе, АС = 30-35 ед./мл.
Готовая к сдаче в
производство культура должна иметь следующие показатели: рН 7,0±0,5, АС = 40
ед./мл. Обязательным условием является отсутствие посторонней микрофлоры.
В случае инфицирования
растущей культуры выращивание следует остановить и содержимое ферментатора
стерилизовать при 0,2 МПа в течение 2 часов. Инфицированная культура подается на
биологическую очистку.
Количество инфицированных
ферментации не должно превышать 5% от всего количества ферментации.
Производство ферментов глубинных культур других микроорганизмов
Кроме ферментных препаратов Глюкаваморин
Гх-466 и Амиломерезентерин Гх-467 в спиртовом производстве можно применять
препараты и других культур микроорганизмов—продуцентов амилолитичсских
ферментов, например Амилодиастатин Гх (продуцент Вас. diastaticus), Глюкобататин Гх (продуцент Asp. batatae), Глюкоэндомикопсин Гх (продуцент
End. biospora),
Амилоризин Гх (продуцент Аsp. oryzae) и др.
Принципиальная
технологическая схема производства этих ферментных препаратов аналогична представленной
на рис. 1. Отличия определяются только биологическими особенностями
микроорганизмов. Они касаются методов ведения посевного материала и состава
питательных сред для лабораторных условий, количеств посевного материала,
состава питательной среды и режима его выращивания в производственных условиях
(рН, температура, продолжительность, количество воздуха, частота вращения
мешалки).
Все эти условия
регламентированы. Регламенты на производство указанных культур ферментов разработаны
ВНИИПрБ.
Ниже приводятся составы
питательных сред и режимы производства ферментов глубинным способом в производственных
ферментаторах наиболее часто встречающихся на производстве культур End. biospora, Asp. batatae-61 и Вас. diastaticus.
Производственная питательная
среда для культивирования фермента End. biospora имеет следующий состав (в %):
Кукурузная мука 2,5
Соевая мука 1,5
Кукурузный экстракт 1,5
Дигидроортофосфат калия (днаммонийфосфат) 0,5
Подсолнечное масло или китовый жир (пеногаситель) 0,05
Вода 93,95
Режим выращивания следующий:
температура среды 26—28° С, продолжительность 72—84 ч, частота вращения мешалки
200— 220 мин-1, расход стерильного воздуха 20—30 м3/ч на
1 м3 среды.
При выращивании культуры
гриба Asp. batatae-61 питательная среда имеет следующий состав (в %):
Мука 1,5
Кукурузный экстракт 0,5
Нитрат аммония 0,5
Карбонат магния 0,2
Обогащенная питательная среда содержит следующие
компоненты (в % по массе):
Кукурузная мука 4,0
Нитрат аммония 1,0
Кукурузный экстракт 0,5
Карбонат кальция 0,2
Карбонат магния 0,2
Режим выращивания следующий:
температура среды 30—32° С, продолжительность 60 ч, расход воздуха па аэрацию
при использовании лучевых аэраторов 15—20 м3/ч па 1 м3
среды.
При выращивании термофильной
бактериальной культуры Вас. diastaticus питательная среда имеет
следующий состав (в % по массе):
Кукурузная мука
0,6
Карбонат кальция 0,2
Нитрат аммония 0,4
Кукурузный экстракт 0,5
Вода 98,0
Для доведения рН среды до 7,0
в нее добавляют раствор карбоната или гидроксида натрия.
Режим выращивания следующий:
температура среды 60—62° С, продолжительность 6—8 часов, расход воздуха при
распылении через форсунку 40 м3/ч на 1 м3 среды.
Температура подаваемого стерильного воздуха 60—65° С, давление в ферментаторе
0,015—0,020 МПа.
НОРМЫ РАСХОДА СЫРЬЯ, ВСПОМОГАТЕЛЬНЫХ МАТЕРИАЛОВ, ВОДЫ, ПАРА, ЭЛЕКТРОЭНЕРГИИ, СЖАТОГО
ВОЗДУХА ПРИ ПРОИЗВОДСТВЕ ФЕРМЕНТОВ - КУЛЬТУР ПЛЕСНЕВЫХ ГРИБОВ
При произаодстве и получении глубинной
культуры препарата Глюкаваморин Гх-466 установлены следующие нормы расхода
(регламентируемые/нормируемые) (в пересчете на 1 тонну условной глюкоамилазы):
Мука кукурузная, кг 1513,5/1589,5
Автолизат дрожжевой, г 8,4/8,9
Солод пивоваренный ячменный, кг 45,405/47,425
Масло подсолнечное, кг 2,58/2/88
Вода, м3
на приготовление пита тельной среды 3,175/3,345
Вода, м3
отработавшая 220/231,0
Вода, м3
загрязненная 1,0/1,05
Сжатый воздух, м3
(23400—46800)/(24570—49140)
Электроэнергия, кВт-ч 2000/2100
Пар (давлением0,5 МПа), кг 5000/5250
Кислота серная, кг 0,5/0,52
Известь хлорная, кг 2,2/2,3
Хлорамин «Б», г 25/26
Формалин, кг 2,5/2,6
При получении глубинной
культуры препарата Ампломезентерин Гх-467 (в пересчете на 1 м3):
Агар, кг 0,01
Мясо-пептонный бульон (МПБ),
л 0,5
Мука кукурузная, кг 60
Экстракт кукурузный
сгущенный, кг 10
Диаммоннйфосфат, кг 9
Карбонат кальция, кг 2
Масло подсолнечное, л 0,5
Кислота, л
соляная 0,0082
уксусная 0,058
Крахмал растворимый, кг 0,010
Ацетат натрия, кг 0,082
Гидроксид натрия, кг 0,033
Иод, кг 0,005
Иодид калия, кг 0,005
Спирт этиловый
рсктификованный, л 0,1
Хлорамин «Б», г 350
Вода, м3
на приготовление питательной
среды 0,966
условно-чистая 22
загрязненная 0,22
Сжатый воздух, м3
на аэрацию среды 1600
на отдувку фильтров 53
Электроэнергия, кВт-ч 90
Пар для стерилизации, кг 483
|