Для переработки картофеля на крахмал используются разнообразные технологические схемы, оснащенные различными видами применяемого для этих целей оборудования. Однако независимо от аппаратурного оформления каждый из этих способов включает стадии производства, которые свойственны всем современным технологиям картофельного крахмала:
-
хранение картофеля,
-
подготовка картофеля к переработке,
-
измельчение картофеля,
-
выделение картофельного сока и мезги,
-
очистка крахмала,
-
утилизация побочных продуктов при производстве картофельного крахмала.
Наиболее эффективной является технология переработки картофеля на крахмал с использованием многоступенчатой гидроциклонной установки. На гидроциклонной установке осуществляются операции разделения тонкоизмельченной картофельной кашки на крахмальную суспензию и смесь мезги с картофельным соком. По техническим характеристикам и технико-экономическим показателям гидроциклонная установка многократно превосходит в совокупности все виды оборудования, применяемого на операциях от начала разделения картофельной кашки до получения очищенной крахмальной суспензии и побочных продуктов в виде смеси мезги и картофельного сока.
Совмещение по новой схеме в одной установке операций разделения и размывки крахмала позволяет в 4-5 раз уменьшить производственные площади под размещение равнозначного по мощности технологического оборудования, а также на 3-4% повысить коэффициент извлечения крахмала из картофеля путем как уменьшения числа ступеней обработки картофельной кашки, так и интенсификации производственного процесса в целом, а также снижения количества сбросов и расхода свежей воды.
Для получения сухого крахмала предусмотрено механическое обезвоживание сгущенной крахмальной суспензии с последующим удалением избыточной влаги методом сушки под воздействием сушильного агента (подогретого воздуха). Схема получения картофельного крахмала рассчитана на комплексное использование всех компонентов перерабатываемого картофеля. Разработаны способы утилизации побочных продуктов - мезги и картофельного сока, одним из которых является получение углеводно-белкового гидролизата и прессованного корма.
Описание и функционирование технологического потока
переработки картофеля сухой крахмал
Согласно технологической схеме (рисунок) для производства крахмала, картофель из оборотного склада подается по гидротранспортеру 2 на камнеловушку барабанного типа 3, далее шнеком 4, в котором происходит отделение транспортерной воды, - на бильную мойку 5. Отмытые от грязи клубни поступают через конвейер-водоотделитель 5а на станцию измельчения, где дважды измельчаются в кашку на терках 6, 7. Терка для картофеля представляет собой аппарат, где измельчение осуществляется за счет истирания клубней картофеля специальными зубчатыми пилками, укрепленными на поверхности барабана, вращающегося с большой скоростью внутри металлического корпуса. Картофельные терки комплектуются прижимами и решетками с отверстиями диаметром 2 мм, что обеспечивает высокую степень измельчения. Эффективность работы картофелетерки зависит от окружной скорости пильной поверхности барабана; она характеризуется коэффициентом измельчения, который достигает 90%. При использовании пильчатых терок с окружной скоростью барабана 90 м/с коэффициент измельчения может достигать 95% и более, при этом отпадает необходимость во второй стадии измельчения картофельной кашки.
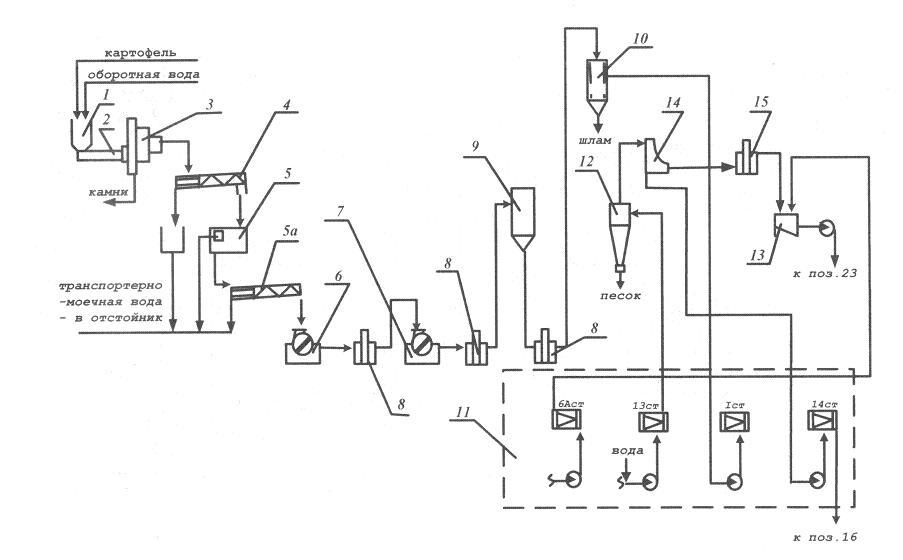
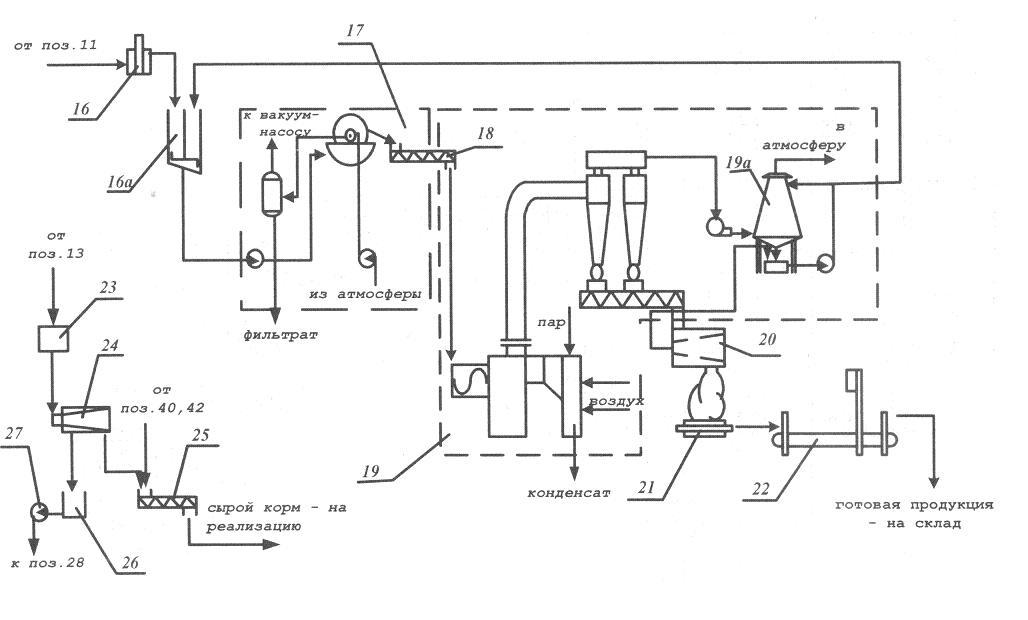
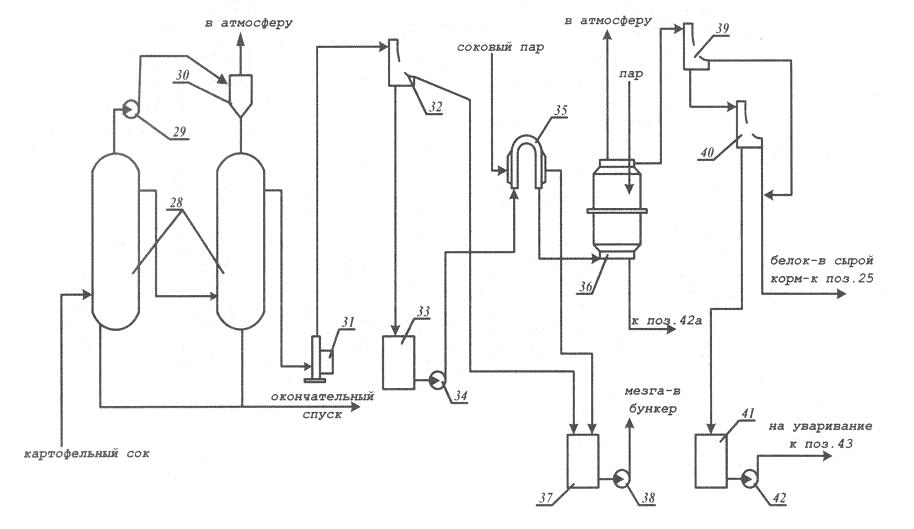
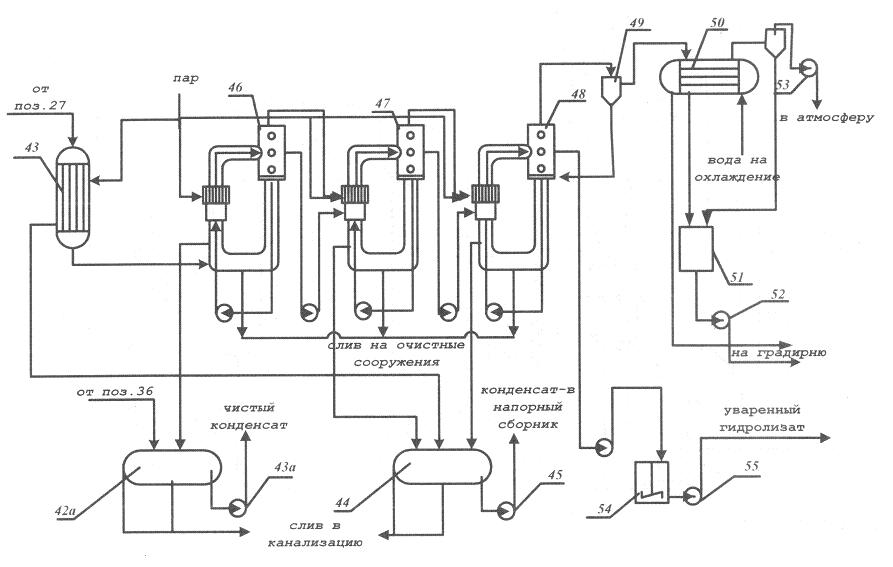
Картофельная кашка из сборника-накопителя 9 через самоочищающиеся фильтры 10, на которых отделяются различные примеси, подается плунжерным насосом 8 на гидроциклонную установку 11, состоящую из 14 ступеней гидроциклонов, из которых 6 ступеней являются обескрахмаливающими, а 8 - промывными.
Работу гидроциклонной установки для выделения крахмала регулируют таким образом, чтобы поступающая на промывание крахмальная суспензия имела концентрацию 6-8, сгущенный сход с последней ступени - 35-40, а смешанные жидкие сходы с I и II ступеней - 1,0-1,5% СВ. Давление в мультициклоне поддерживают на уровне 0,3-0,4 МПа. Крахмальная суспензия с 13-й ступени гидроциклонов подается на песковый гидроциклон 12 (единичный), затем на рафинировальное дуговое сито 14 для выделения мелкой мезги и далее на 14-ю ступень. Очищенная крахмальная суспензия поступает для обезвоживания до концентрации 64% СВ на установку барабанного вакуум-фильтра 17, откуда сырой крахмал винтовым конвейером 18 направляется в пневматическую сушилку для крахмала 19.
В основу работы сушилок для крахмала пневматического типа положен принцип сушки разрыхленного крахмала в движущемся потоке горячего воздуха; при этом скорость движения смеси крахмал-воздух по сушильному тракту должна быть больше скорости витания зерен крахмала в потоке. Практически сушка крахмала длится доли секунды, т.е. происходит почти мгновенно. Особенности конструкции и работы пневматической сушилки для крахмала, автоматизация сушки позволяют применять воздух, нагретый до высоких температур. Температура сушильного агента калориферов, входящих в состав сушильной установки, составляет 140...150°С, однако крахмальные зерна за счет испарения поверхностной влаги не успевают нагреться выше 60° С.
Разделение сухого крахмала и воздушно-паровой смеси происходит в циклонах; окончательную очистку воздуха от крахмала осуществляют мокрым способом в скруббере 19а.
Высушенный до требуемой (равновесной) влажности крахмал может содержать некоторое количество крупки, образующейся при переработке недоброкачественного сырья, которую отделяют на ситовом аппарате типа бурата 20, разводят и направляют в основное производство для переработки. Очищенный сухой крахмал из бурата затаривается в мешкотару, затем взвешивается на весах 21 и зашивается на мешкозашивочной машине 22.
При утилизации побочных продуктов от производства картофельного крахмала по комбинированной схеме вырабатывается уваренный углеводно-белковый гидролизат и белковый корм. По этой схеме картофельный сок из сборников 28, оснащенных вентилятором-пеногасителем 29, насосом 31 подается для очистки от мезги на сито 32, а затем из сборника 33 насосом 34 откачивается через подогреватель 35 (t=60 С) в коагулятор 36. Отсюда он поступает для отделения белка на дуговые сита 39, 40. Осветленный картофельный сок из сборника 41 направляется на уваривание на трехкорпусную выпарную установку 46, 47, 48 и из неё откачивается насосом в сборник 54. Для конденсации паров из третьего корпуса 48 установки используется поверхностный конденсатор 50. Разрежение в выпарной установке и конденсаторе создается вакуум-насосом 53. Конденсат из конденсатора 50 и ловушки 49 поступает в барометрический сборник 51 и насосом 52 откачивается на градирню, где охлаждается и используется вторично для конденсации паров. Конденсат из первого и второго корпусов установки собирается в сборниках 42а и 44.
Наиболее простым способом утилизации мезги и картофельного сока является либо использование их смеси в качестве корма для животных, либо разделение этой смеси на центрифуге 24 на две фракции: мезгу, используемую в качестве корма, и картофельный сок, направляемый в пруд-накопитель для последующего удобрительного полива сельскохозяйственных угодий.
Основные характеристики сырья и готовой продукции при переработке картофеля на крахмал
Для получения высоких технико-экономических показателей в производстве крахмала необходимо перерабатывать картофель высококрахмалистых сортов, что позволяет снизить его расход на получение 1 т крахмала, а следовательно, и его себестоимость. Согласно действующим нормативам, картофель, поступающий на переработку, должен иметь крахмалистость не менее 13, а засоренность после мойки - не более 0,1%.
Крахмал сухой картофельный должен вырабатываться в соответствии с нормативной документацией (НД); к числу основных показателей его качества относятся: цвет, запах, массовая доля влаги (не более 20%) и др.
В нормативной документации, разработанной во ВНИИ крахмалопродуктов, отражены технологические режимы и качество побочных продуктов производства картофельного крахмала: углеводно-белкового гидролизата и белкового корма.
Углеводно-белковый гидролизат - густая коричневая масса, состоящая
из элементов:
-
углеводы (в том числе редуцирующие сахара), % СВ...........65-66
-
протеины, % СВ, не
менее........................................
16 (N х 6,25)
-
минеральные вещества, %
СВ.....................................13-14
Белковый корм имеет следующий состав:
-
углеводы, % СВ........................................................40-41
-
протеины, %
СВ не менее........................................................ 20 (N
х 6,25)
-
Клетчатка, %
СВ ..................................................................... 30-32
-
прочие
вещества, % СВ .......................................................... до
10
Углеводно-белковый гидролизат может быть использован в производстве этилового спирта без предварительного упаривания путем добавления на стадию замеса или в качестве биостимулятора при выращивании кормовых дрожжей, либо в хлебопечении как заменитель красного ржаного солода.
|